Planes
Content
Expert knowledge - Planes
Advantages:
- Warm and pleasant to touch
- Gentle to workpiece, no discolouration of wood
- Light weight prevents tiring
Disadvantages:
- High sole wear with heavy loading
- Warping may occur
- Little resilent mass, less-smooth operation with difficult grains
Advantages:
- Operated by pulling, giving good control – gentle to the joints and less tiring
- Smoother operation thanks to thick blade
- High plane-blade quality
Disadvantages:
- Take longer to set up (does not apply to planes with replacement blades)
- Possible warping due to atmospheric influences (does not apply to planes with stabilised bodies and replacement blades)
- No mechanical adjustment aids for plane blade and mouth
Advantages:
- High wear resistance of sole base and edge of mouth
- No warping of plane body due to atmospheric influences
- High momentum: smoother running, even with difficult grains and knots
- Simple adjustment of plane blade and usually also of mouth opening
Disadvantages:
- Heavier, so tiring for larger planing jobs
- Can rust (not with bronze planes)
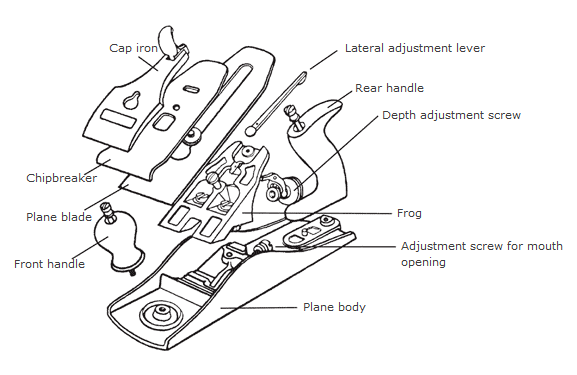
There are three types of metal planes: »bevel-up« planes, »bevel-down« planes and scraping planes.
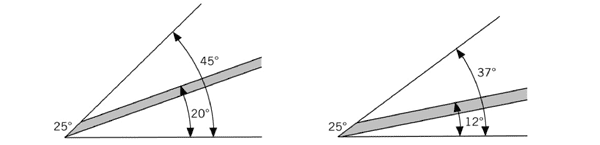
The »bevel-up« plane evolved from the block plane - a one-handed plane previously used for planing cross-slots into posts to accommodate blockings for reinforcement. Hence the name »block plane«.
But back to the bevelup as the distinguishing feature. Basically, the blade in the block plane is mounted the opposite way round from that of a conventional »bevel-down« plane
The reason for this is the small size of the block plane, which made it impossible and unergonomical to use a normal frog. The problem was solved quite simply by changing the angle and direction of the blade to produce the same cutting angle as in a bevel-down plane. The bevel-up principle is less widespread due to the poor quality of cast iron in the early Stanley planes. Subject to extreme forces where the blade sits at the mouth of the sole, the cast iron on these planes broke easily. Today, however, better cast iron makes for much more stable plane bodies that are more resistant to the forces of »bevel-up« planing.
Advantages and disadvantages:
- Easily adjustable cutting angle
The major advantage lies in the easily adjustable cutting angle. Because the bevel angle on the blade affects the cutting angle, the plane can be optimised by altering the bevel angle on the blade - most easily done with a micro or secondary bevel.
- No chipbreaker
The chipbreaker, which usually adds stiffness to the blade, is missing on bevel-up planes. Therefore the iron used is much thicker.
- Thicker blade
The blade on a bevel-up plane is thicker than that of a bevel-down plane. This is an advantage, as it leads to smoother surfaces and chatters less.
- Low centre of gravity
Also an advantage is the low centre of gravity, which is created by the low-angle frog.
- Plane body and blade support from a single piece
In »bevel-down« planes an additional frog in the plane body supports the blade.
In »bevelup« planes, the plane body and blade support are made from one piece, enhancing overall stability.
- Simple mouth adjustment
»Bevel-up« planes have a screw at the front end for adjusting the mouth opening easily. The cutting depth remains unaffected.
- Reduced weight
The absence of the additional frog makes »bevel-up« planes lighter than »bevel-down« ones.
- No lateral adjustment
The »bevel-up« version works without a lateral adjustment screw, which may be considered a disadvantage. As with the wooden plane, the blade is adjusted by tapping lightly on its sides.
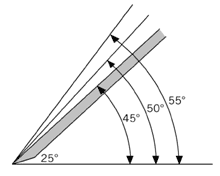
The renowned plane inventor Leonard Bailey, who worked for Stanley in his day, was a major influence on modern plane design. Stanley enhanced his system with its Bedrock Design, which enables the frog position to be modified without loosening the blade fixture. With the exception of a few minor adjustments, his design has remained unchanged ever since. Only the blade-adjustment mechanism has been modified. It was revolutionised by Thomas Norris, who introduced a single screw for adjusting both the cutting depth and the blade angle. Experts continue to discuss the advantages and disadvantages of this system, as, with the Bailey-type adjuster, adjustments can be made while planning through a low central adjustment mechanism.
Advantages and disadvantages
- Cutting angle depends on frog angle
The cutting angle is more easily adjusted in »bevel-up« than »bevel-down« planes. However, frogs with different slope angles are available for Lie Nielsen planes.
- Simple lateral blade adjustment
Lateral adjustment of the blade is easily done via the adjustment lever.
- Full blade support
The frog provides a smooth and large seat for the whole blade, reducing chatter to a minimum.
- Additional weight
Additional weight means the plane sits solidly on the surface. This is particularly advantageous for working with irregular grains and wood that is difficult to plane.
- Adjustment of mouth opening changes cutting depth
Because the frog runs on an inclined surface, any adjustment to the mouth also affects the cutting depth. This can be counteracted by turning the central adjusting mechanism.
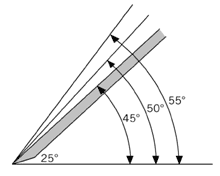
Scraping planes arose from the idea of embedding a scraper into a plane body for more convenient use. Usually, a hook on the blade is used for scraping. The blade has to be ground perfectly angular to raise the hook, which is applied to the upper edge of the bevel with the burnisher, much like a scraper. Tools with thick blades (by Lie Nielsen) do not require a hook but are also used with one. Those with thinner blades (made by Kunz and Veritas) generally use the raised hook.
Their blades still have a bevel (30°-45°), which reduces the amount of material needing to be »displaced« when raising the hook. The principle of scraping with a hook differs greatly from cutting with a blade.
Normally, the depth is determined by the hook and angle. These planes are indispensable for achieving tear-out-free surfaces on difficult woods and grains (primarily hardwood).
When should the different cutting angles or blade angles be used?
- Cutting angle 36-38°
Preferred for end grain, where less tear-out is to be expected because the fibres break easily. With this cutting angle, the fibres are actually cut off. When planing along the grain, you should only take fine shavings with a small mouth opening to prevent premature splitting of the wood.
- Cutting angle 43-46°
Normal cutting angle for general work with relatively low cutting resistance.
- Cutting angle 50-60°
On highly figured wood this angle creates less tear-out, by breaking the fibres before they split. A disadvantage is that the iron will cut less and scrape more which dulls the iron more quickly.
- Blade angle 75-100° (cutting angle is defined by a raised burr)
At this angle, you scrape instead of cutting (scraping plane). Since this type of planing causes minimal tear-out, it is ideal for wild grain structures and woods that are difficult to plane.