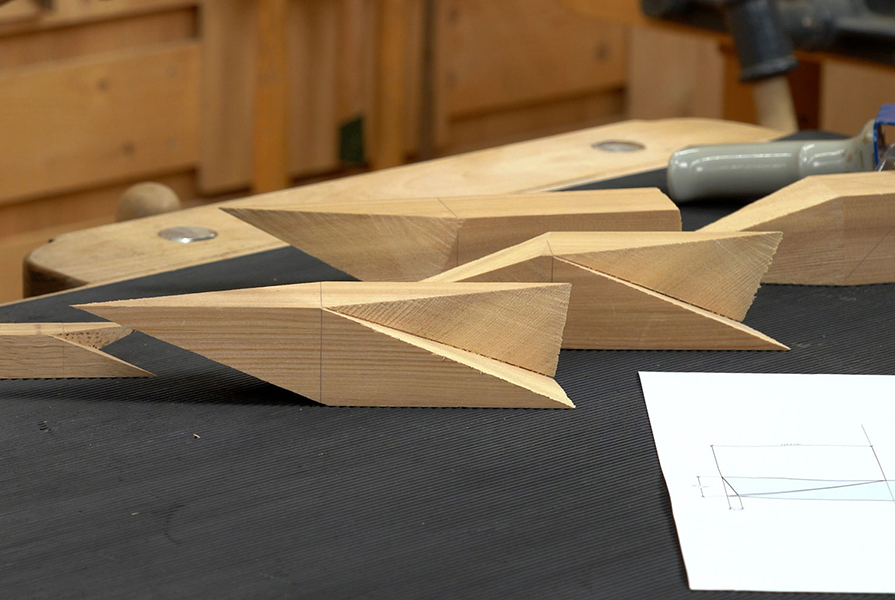
In a recent DICTUM course workshop, while hand sawing the Japanese lengthening joint "sumi isuka tsugi" – in English described as the "quadruple-faced halved rabbeted oblique scarf joint", the question arose whether this joint could also be cut by machine. As we had been asking this our-selves for some time, we decided to investigate.
Trial and error
Our first idea was to cut the joint with a rebate bit. This requires the workpieces to be run along the rebate bit at a doubly slanted angle. That in turn meant we had to design and make an appropriate support for the workpieces. After several "trial and error" attempts it became clear that even mak-ing the support is no straightforward matter. We ended up using a CAD program to design a sup-port that enabled us to transfer the precise angles to the workpiece. To save having to set and re-set the machines multiple times, we sawed the support to size by hand.
To allow the workpieces to be accurately positioned in the support they were marked with refer-ence lines and the would-be oblique scarf joint was then machine cut on a router table using a rebate bit. Three trial pieces were needed before the rebate setting was correct. Initially, the machined joint appeared to be sound. The joint looked tight along the seam and the joined pieces were aligned. But on closer inspection it became apparent that there were internal gaps in the joint. The strength of the glued joint and corresponding load-bearing capacity was therefore very poor.
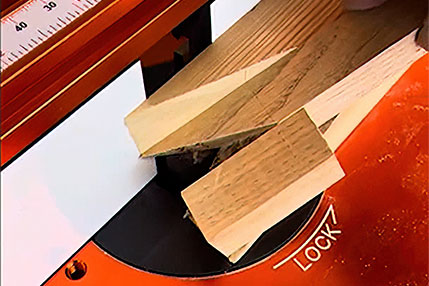
Trial run on router table with rabbeting router and first support piece
So to work out the precise angles of the joint, we drew it from scratch on the computer and then revised the design of the support piece. And lo and behold, it now seemed possible to construct the joint on a circular bench saw with the saw blade set at an angle. The required angle could be taken from the drawing. Again, several trial pieces were required before the machine was precisely aligned and set up. The support had to be reworked too. With this approach, we were finally able to precisely construct the sumi isuka tsugi, aka quadruple-faced halved rabbeted oblique scarf joint, using a circular saw.
Can the Japanese joint sumi isuka tsugi be cut by machine?
The answer to the original question whether a sumi isuka tsugi joint can be cut using a machine is certainly "Yes". But does this approach make sense?
This lengthening joint always needs glueing. It's intended use is to lengthen short sections of wood. This means it's only used when there's a scarcity of wood. When planning the machine-cutting of this joint, including designing and making the required support piece, a lot of time was spent and several trial pieces were used before everything fitted..
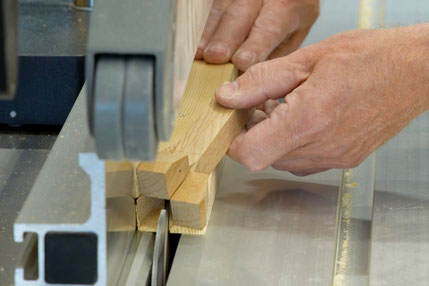
Cutting the joint using a circular saw requires considerable effort
So if you are able to saw precisely and can follow a marked line with a Dozuki, then it's much easier to cut this joint by hand. Marking out the joint is very easy and doesn't take long. Only four cuts are required on each of the two workpieces to be joined. After a total of eight cuts the hand-crafted joint is complete. The payback is that you have extended your usable wood supply and have done this in a very inconspicuous manner. Less noticeable than any other type of scarfing.
Give it a go if you want, but take care!
For those of you who would like to have a go at machine-cutting this joint we have provided the dimensions of our support piece here:
The support piece we used is intended for extending wood with a cross-section of 20 x 20 mm. The saw blade should be tilted by 4°.
Be mindful of your safety! Please use a clamp to firmly secure your workpiece to the support. Al-ways bear in mind the dangers of working with a stationary machine.
If you are successful in using the method we have described here, or if you discover your own, perhaps more clever solution for making this or any other Japanese wood joint with the help of a machine, then please send the details of your results to the DICTUM craft gallery.
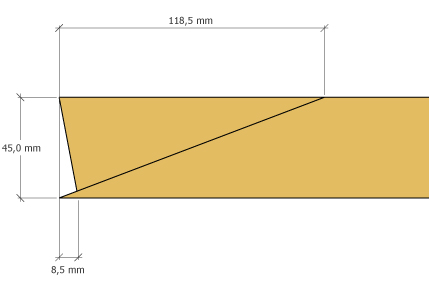
The precise dimensions of the support depend on the workpieces to be joined